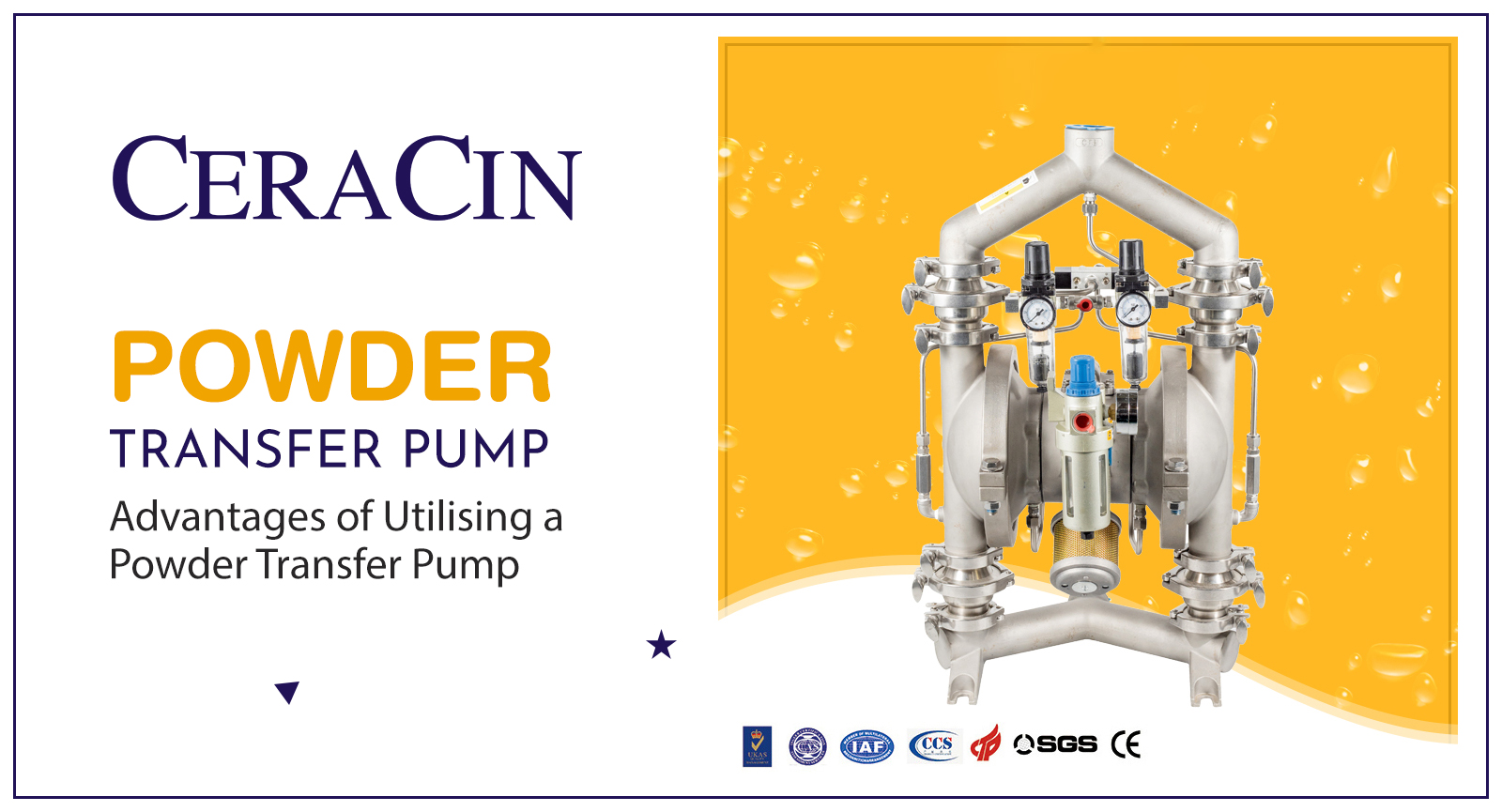
Advantages of Utilising a Powder Transfer Pump
Many industrial operations, including plastics processing, chemical processing, pharmaceutical manufacture, and food and beverage production, need the transport of powder materials. Companies employ a variety of methods to transfer powder products, including physical labor in buckets or containers, Powder Transfer pumps, screw feeders, and mechanical or pneumatic conveyors. Here we’ll talk about Powder Transfer Pumps and their advantages.
Powder Transfer Pump
Air-operated diaphragm (AODD) powder transfer pumps function similarly to a portable vacuum cleaner, with a suction hose sucking in and a discharge hose discharging powder out at the same time. AODD pumps for powder transfer can increase safety and give significant cost savings.
How Does a Powder Pump Work?
Powder pumps use pressurized air to move diaphragms inside the pump housing. These diaphragms operate together to trap fluid on one side while forcing an equal amount of fluid out of the discharge hole.
In addition, the pump then recycles air that exits the pump via the air exhaust, which is fed back into the pump by the valve balls, dispersing any powder that collects as the valve balls open and close.
The Benefits of Powder Transfer Pump
AODD powder transfer pumps offer numerous operational advantages over other powder transfer systems, including the following:
Compact
Pneumatic powder conveying systems use flexible pipes to accommodate various infeed and destination points as well as longer conveying distances. This makes them a compact system that takes up less area when compared to mechanical conveying methods.
They are quick to install and use due to their simple design. They are also a cost-effective choice for transporting from many pick-up places on a wide scale.
Hygienic
Powder transfer systems assist limit the danger of product contamination by having crevice-free surface designs that prevent powders and material from being lodged. It also removes outside impurities, keeping the facility and equipment clean. Additionally, the powder transfer equipment is made of stainless steel and has FDA-compliant seals. Additionally, the pipe can be CIP cleaned and dried.
Dust-Free atmosphere
Because the product is moved through an enclosed pipeline, it contributes to a dust-free atmosphere that supports the health and safety of all facility employees. Contained powder transfer reduces the requirement for manual solids handling, hence protecting the operator from exposure.
Process Efficiency
Pneumatic powder conveying equipment is more streamlined, which improves transfer efficiency. It takes fewer people, and hoists and handling equipment over the reactor are no longer necessary.
Quick Transfer
In addition to process efficiency, powder transfer equipment delivers quick transport efficiency by using clean, non-lubricated compressed air.
Low maintenance and longer equipment life
These systems have fewer moving parts than mechanical conveying systems, necessitating less maintenance. Fewer moving parts also mean less wear and tear. Similarly, the equipment’s closed system reduces the possibility of damage and deterioration to the agitator and seal system during the mixing operation, extending its life.
Product Quality
This system’s tight environment efficiently eliminates exterior impurities, which helps to maintain product quality. It also prevents product leakage, and some types can stop de-mixing.
To Finish
To maximize benefit and function properly, the powder must be fine-grained, fully dry, free-flowing, and have a low bulk density. The powder must be fluid enough to flow through the pump, with the flow rate and distance defined by the powder type, weight, bulk density, form, and size.
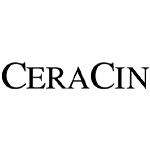
Ceracin
Ceracin has expertise in industrial pump manufacturing since 2016. We are committed to provide our nation with the highest quality pumps at competitive prices.