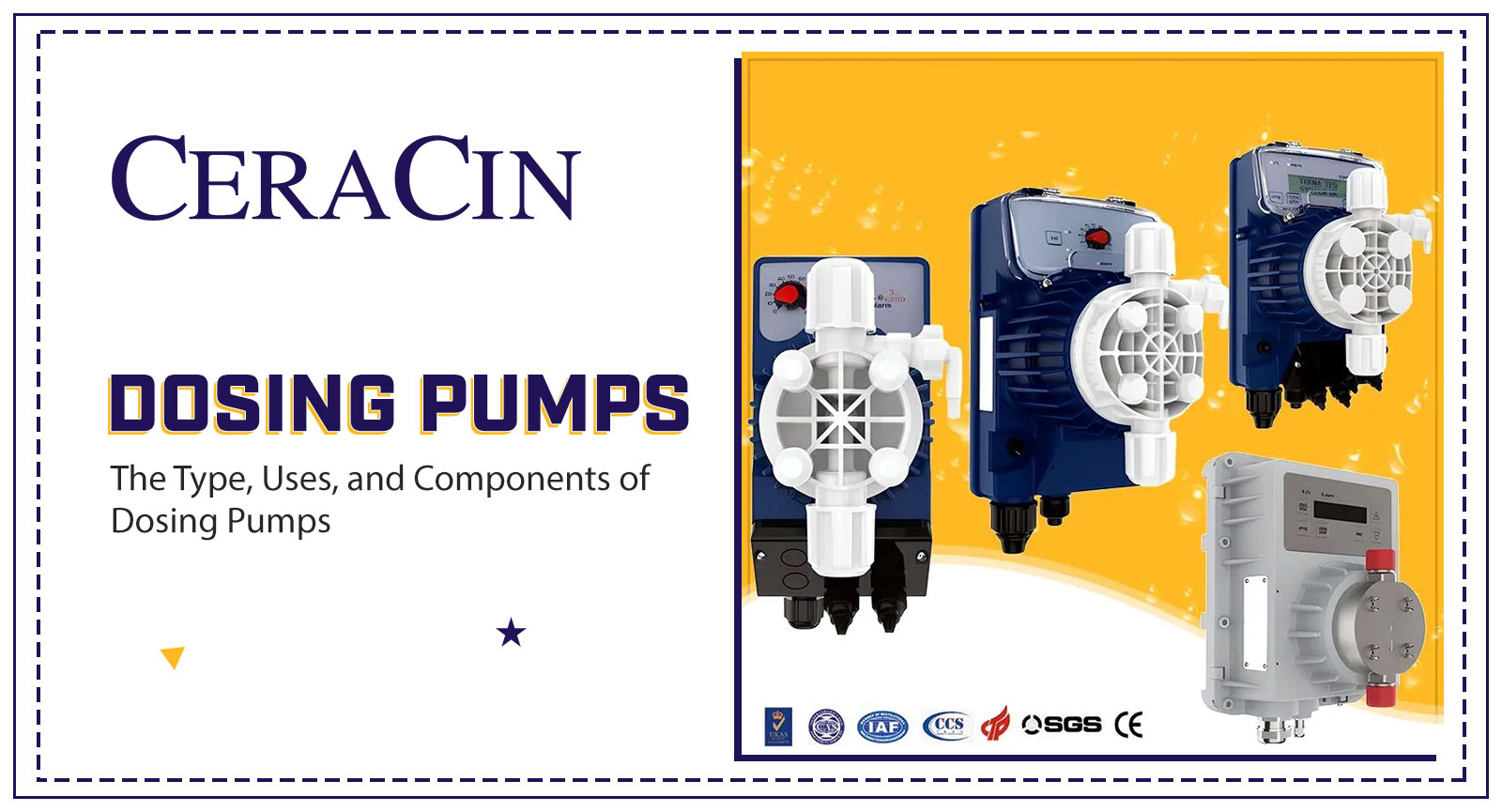
The Type, Uses, and Components of Dosing Pumps
A dosing pump is a positive displacement pump, built to inject a chemical or other material into a flow of water, gas, or steam. These pumps enable a highly accurate flow rate for maximum control in an integrated system. This pump is used in a wide range of applications and industries, from wastewater treatment, and chemical to food processing. This blog post explains the different types of dosing pumps and their uses.
How does a dosing pump work?
A dosing pump sucks a predetermined volume of liquid into its chamber before injecting the chemical into a tank or pipe containing the fluid being dosed. It is driven by an electric motor or an air actuator and contains a controller that switches on and off the pump and regulates the flow rate. Some versions have more complex control systems.
What are the different types of dosing pumps?
These four dosing pump types are used for various chemicals and uses. They differ according to pumping action and mechanism.
Diaphragm (constant injection) pumps employ a diaphragm, piston, and valves on both the inlet and output to fill and empty their chambers. Drawing in the piston fills the chamber, and a predetermined amount of chemical is injected at a specified speed, often a percentage of the maximum flow rate. Certain pump types are capable of varying dosage rates.
Diaphragm (pulse injection) pumps likewise employ the diaphragm mechanism, but instead of a steady flow rate, a solenoid coil receives the chemical and injects it in pulses. The flow rate is the amount of time between pulses. It is less precise than a continuous injection pump, but it is simpler to construct and less costly.
Lobe pumps allow a specific volume of fluid to flow through meshing gear impellers. It is not as precise as a diaphragm pump and is only appropriate for high-viscosity fluids that self-lubricate to reduce wear. They are not designed for low flow rates since it is difficult to assure accuracy.
Peristaltic pumps are quite precise in dosing. A flexible bent tube allows the fluid to pass through, and the flow is regulated by a roller that moves via a mechanical arm on the outside. This forces the product from the tube into the dosing tube and the main fluid stream.
What are the components of a dosing pump?
The three major components of a chemical dosing pump are an injector, a metering pump, a foot valve, a chemical tank, and a control system.
Injector Assembly
This is a valve used to inject chemicals into the flow. It is a non-return valve built to withstand pip pressure. This allows for appropriately mixing chemicals into the liquid or product in defined doses. It is self-actuating, which helps to prevent backflow. This helps to reduce waste and maintain the correct combination.
Metering Pump
All metering pumps include an inlet, dosing, and suction lines. The dosing pump’s size might vary depending on the use. The pump comprises different materials such as rubber, plastic, or stainless steel. Everything is determined by the project’s purposes and requirements.
Foot Valve
This is a one-way valve linked to the suction pipe. In most cases, it is located in the product drum. It uses a float switch to check for product availability. When the product is unavailable, an alert will ring.
Chemical Tank
Tanks exist in a variety of sizes and kinds, depending on the application. When handling hazardous chemicals, some tanks will require particular ingredients to guarantee proper functioning. To protect the facility’s and its personnel’s safety, toxic or flammable combinations must be properly stored.
Control System
Most plant owners utilize computerized control systems to achieve maximum efficiency. They do, indeed, automate some system processes. Whether it is a commercial water booster pump system or a chemical dosing pump, depending on automated systems allow plant owners to maintain a high level of production and efficiency.
These systems are powered by sensor control systems. They can identify variations in mixture, pressure, and flow. They can also be used to automate modifications to each to keep their readings accurate while in operation.
Ceracin is a leading brand of pumping systems that can assist you choose the best dosing pump for your needs regardless of the size of your project. Contact our team for further details.
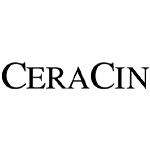
Ceracin
Ceracin has expertise in industrial pump manufacturing since 2016. We are committed to provide our nation with the highest quality pumps at competitive prices.